SSMS Nonwoven Fabric Making Machine
SSMS is composed of spunbonded nonwoven fabric + spunbonded nonwoven fabric + meltblown nonwoven fabric + spunbonded nonwoven fabric.
Compared to SMS, it offers softer and more uniform nonwoven fabric, making it particularly suitable for hygiene applications. It can be used for the top sheet, core wrap, back sheet, and other components of diapers and sanitary napkins
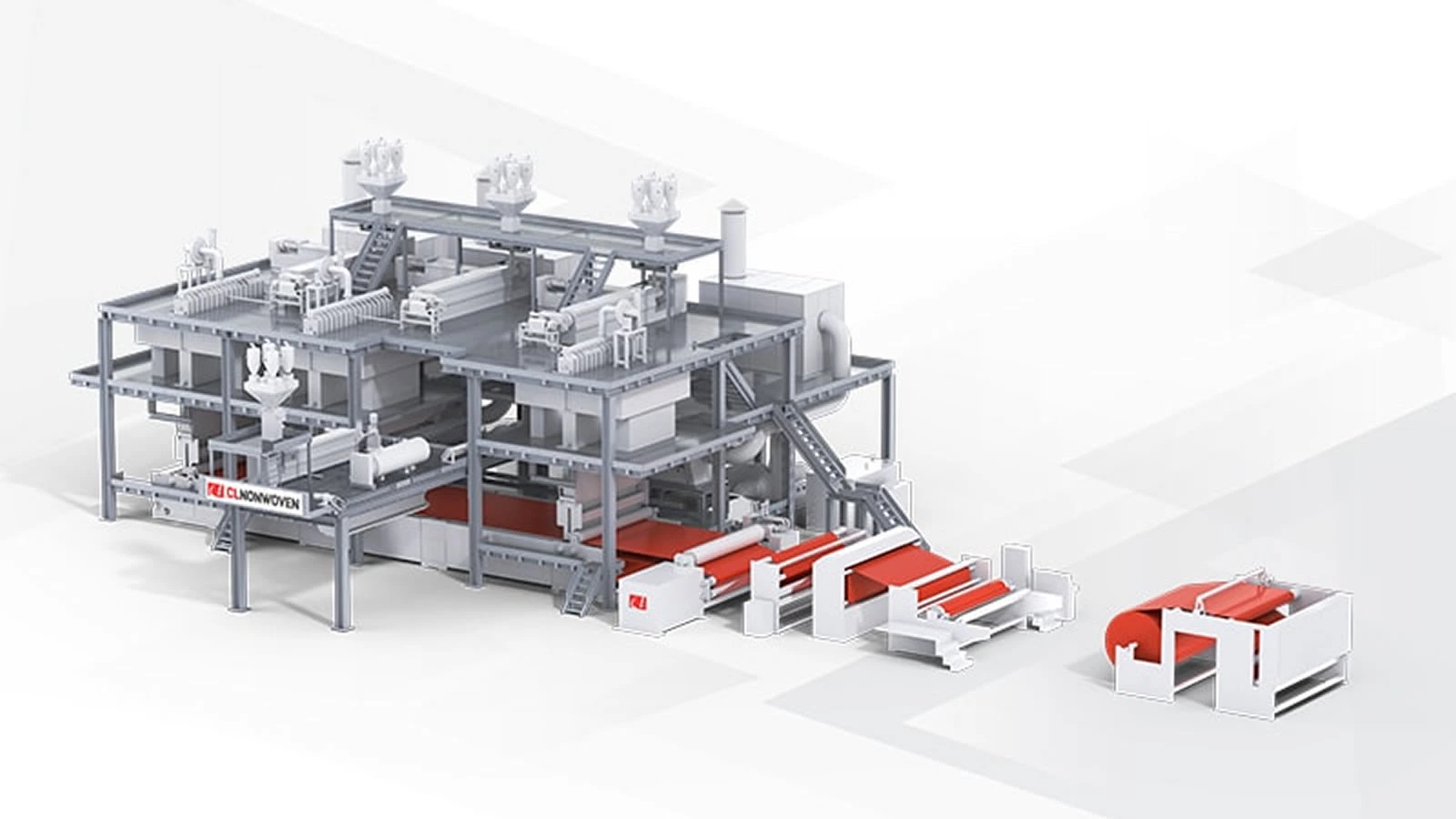
SSMS Nonwoven Making Machine Technical Specification
Model | Effective Width | Fabric Gsm | Machine Speed | Raw Material | Capacity |
1600 SMSS | 1600 | 8-80gsm | 650m/min | PP Chips | 16.5 Ton/Day |
2400 SMSS | 2400 | 8-80gsm | 650m/min | PP Chips | 24.5 Ton./Day |
3200 SMSS | 3200 | 8-80gsm | 650m/min | PP Chips | 33 Ton/Day |
4200 SMSS | 4200 | 8-80gsm | 650m/min | PP Chips | 43 Ton/Day |
PRODUCTION LINE OVERVIEW
This nonwoven fabric manufacturing machine is employed to produce nonwoven fabrics using PP spinning, web forming, and thermal bonding reinforcement processes. By utilizing PP as the primary raw material and incorporating additives like color master batches, antioxidants, anti-pilling agents, and flame retardants, we manufacture nonwoven fabrics with diverse colors and properties suitable for various applications. This production line can manufacture SS/SSS PP spunbond products and SMSS PP spunmelt products, which can be tailored according to different market requirements and customer preferences.
SMSS sorting: S1 → M → S2 → S3 from the web former to the direction of the calender.
1 Main equipment of spunbond system
1.1 Dosing system
Each system uses negative pressure suction type automatic feed.The feeding pipe is made of stainless steel with 1mm wall thickness. The dosing system provides the process interface to the operating interface of the host equipment for inquiry, and the fault alarm of the dosing system is output to the console of the host equipment for easy checking. 2pcs of material tanks with 2 tons capacity each, and 2 sets of 11KW high pressure suction fan are provided. (S1 and S2 are the same).
1.2 Screw extruder
Function and composition of the equipment: this device is mainly to squeeze and melt the PP chips, composed of transmission gear, reducer, screw, mixing head, sleeve, ceramic heater, frame, etc., and it’s equipped with automatic temperature control, cooling system and alarm system. The main transmission adopts AC frequency conversion control. The temperature control of each area adopts the temperature control module, solid state relay and Pt 100 platinum thermistor to form a temperature control closed-loop system.
1.3 Extruder for recycling materials:
Equipment function and composition: for edge material recycling. It consists of screw, sleeve, discharge head, melt filter, transmission device, heating system, thermal insulation device, frame, temperature and pressure control system, edge material feeding roller and guide wheel device, etc... Using the AC motor frequency conversion speed regulation, the temperature control of each area adopts the temperature control module, solid state relay, Pt 100 platinum thermistor to form the temperature control closed-loop system. The discharge head is equipped with check valve, with the head pressure display, the new type of easy-to-feed and prevents hand injury, the feeding port is controlled by Siemens frequency converter.
3.1.4 Melt filter:
Connected the extruder directly with the flange, composed of two sets of filter units.
1.5 Spin pump and drive (3 sets, CL Latest Design)
Type: gear pump
1.6 Spinning die body (3 sets, CL Latest Design)
Melt distribution method inside the box: single pump, single hanger type
1.7 Monomer suction device
Double row and parallel with multiple tubes
1.8 Quench chamber device (3 sets, CL Latest Design)
Adopting a new type of cross air blowing structure, the main frame is made of aluminum material, and stainless-steel sealing plate with insulation.
1.9 Stretching Unite (3 sets, CL Latest Design)
Adopts a new stretching air duct structure with thermal insulation.
1.10 Diffuser (2 sets, CL Latest Design)
The width of diffusion duct can be adjusted online.
2 MAIN EQUIPMENT OF MELT BLOWN SYSTEM
2.1 Dosing system:
Each system uses negative pressure suction type automatic feed. The effective material feeding height is 12m and the horizontal conveying distance is 60m. The feeding pipe is made of stainless steel with 1mm wall thickness. The dosing system provides the process interface to the operating interface of the host equipment for inquiry, and the fault alarm of the dosing system is output to the console of the host equipment for easy checking.
2.2 Screw extruder
Function and composition of the equipment: this device is mainly to squeeze and melt the PP chips, composed of transmission gear, reducer, screw, mixing head, sleeve, ceramic heater, frame, etc., and it’s equipped with automatic temperature control, cooling system and alarm system. The main transmission adopts AC frequency conversion control. The temperature control of each area adopts the temperature control module, solid state relay and Pt 100 platinum thermistor to form a temperature control closed-loop system.
2.3 Melt filter
Connected the extruder directly with the flange, composed of two sets of filter units.
2.4 Spin pump and drive
Type: gear pump
2.5 Meltblown system spinning die body and spinning components
Design working pressure of the meltblown mold head: 300℃
2.6 Melt pipeline adopts heating and insulation overall mode.
2.7 Steel structure platform (1 set, CL Latest Design)
The steel platform of the meltblown system can be lifted and lowered for adjusting DCD.
The steel platform of the meltblown system can also pan along the CD direction and be offline.
2.8 Meltblown spin belt protection device (1 set, CL Latest Design)
Spin belt protection device for special situations such as unexpected power outage, hot air shutdown, and spin belt stop.
2.9 Stretching Unit heating device
2.10 Blower (Germany or South Korea brand)
2.11 Web former (1 set, CL Latest Design)
Web forming speed: 550m/min
2.12 Hot pressing roller (3 sets)
Driving mode: Passive
2.13 Support roller (3 sets)
The hardness of the rubber layer on the surface shall not be lower than SHA76.
2.14 Driving system (1 set)
The driving bearing adopts NSK or SKF brand, with a journal of 90mm.
2.15 Structure of the web former:
Wall plate type steel plate thickness is 40mm. Protection with cover plates on both sides.
2.15 Two-roll calender (1 set, CL brand)
Production speed: 650m/min
Roller’s form: the upper roller is an embossing roller, and the lower roller is a smooth roller. The effective pattern width of the embossing roller is 3, 700mm. The width of the smooth roller is 3, 800mm.
2.16 Hydrophilic System With Dryer
Double-side Kiss Roll with oil distribution system
2.17 Winder (1 set)
Effective working width: 3, 700mm
2.18 Slitter (1 set)
Effective working width: 3, 700mm