SMS Nonwoven Fabric Making Machine
In 2002, CL launched China's inaugural SMS line.
This SMS non-woven fabric is non-toxic, odorless, and highly effective in preventing bacterial contamination. Through special treatments, it can be enhanced with anti-static, anti-alcohol, anti-plasma, water-repellent, and hydrophilic properties. These qualities make it an ideal choice for sanitary pads, diapers, surgical covers, masks, crop covers, and various other applications
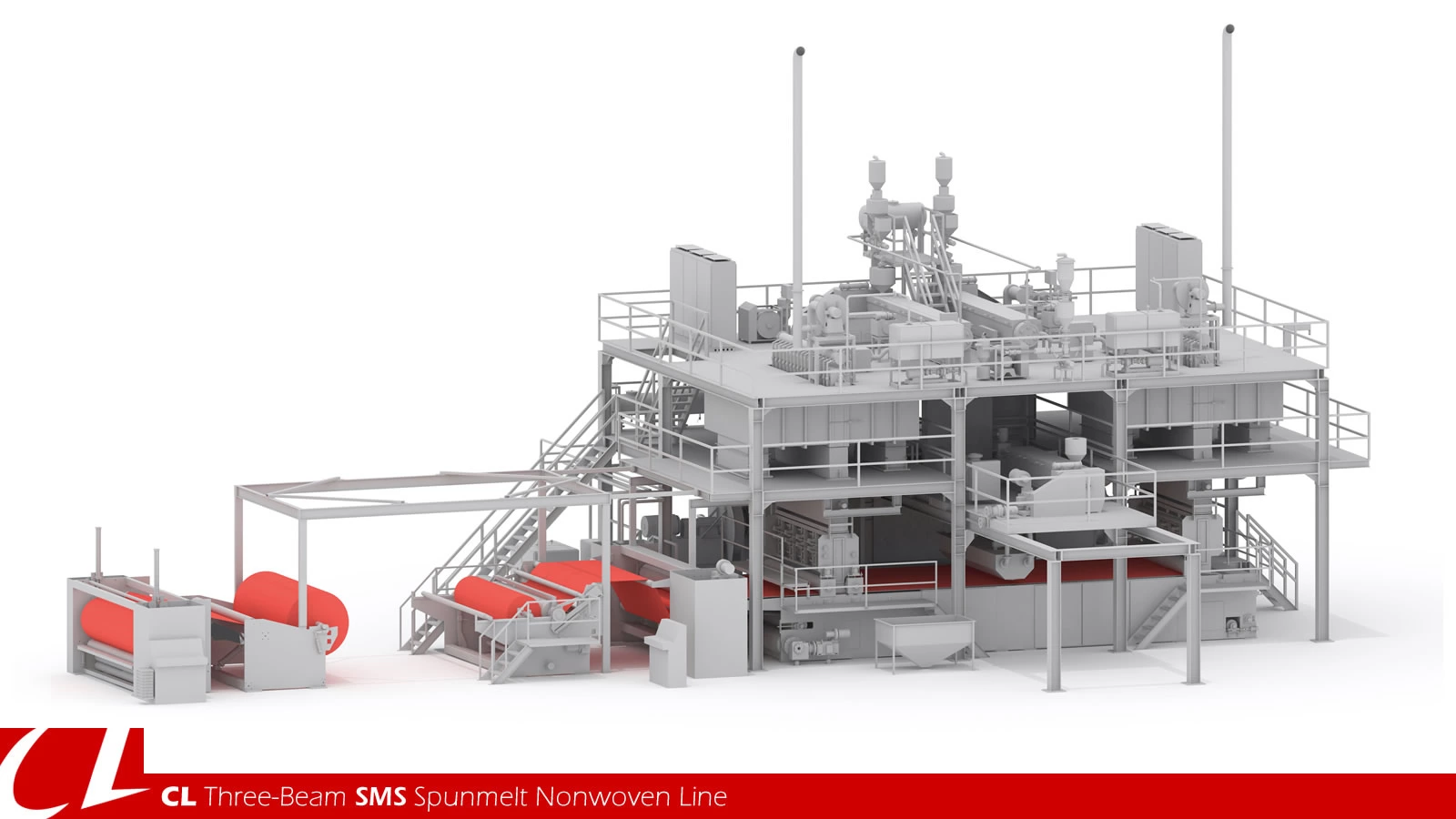
Technical Specification
Part One: The Design Conception Of This Project Is As Following:
PP chips ---- Blending and Feeding --- Melting in the Extruder --- Prefiltration Recycled Materials
Color masterbatch -- Spinning -- Cooling with the Side Wind -- Air DraggingMeltblown
Cooling with the Side Wind -- Air Dragging---Web forming -- Thermal bonding --
Winding -- Cutting -- End Products
From the figure it can be seen that this SMS spunmelt line includes the following parts:
- Engineering: Electricity supply and distribution, Air conditioner and Cooling system.
- Spinning: PP chips feeding, Melt and Extruding, Spinning
- Web: Web forming, Thermal bonding and Winding
- Cutting: Semi-manufactured goods, Cutting, Packing
- Working time is calculated with four groups alternative.
Part Two: Products Specification And Processing
- Products specification : Weight 9-80 g/sqm, width 1600/3200/4200MM
- Quality Standard: According tothe international standard of SMS spunmelt nonwovens.
- Spinning: Feeding System: PP Chips and 10% of the raw material for the colorful PP Articles. Extruder temperature: (Adjusted according to the different MFI of different material)
- Metering Pump: Two pumps
- Web Forming: Uniform at the cross direction, Decreasing from the air jet to the web former at the machine direction.
- Thermal bonding Width: 1600/3200/4200 mm
- Roller Type: The up one surface is fluting and the down one surface is smooth.Bonding area: As per fabric sample
Part Three: M Section
- Raw material feeding system
- Masterbatch feeding
- Extruder
- Spin pump
- Spinning die
- Nozzle
- Air heater
- Air compressor
- Down suction system
Part Four: SS AND M SHARE PARTS
- Winding Max width: 2000mm
- Cutting Effective width: 1600mm
- Max rewinding diameter:1000mm
- Steel platform
Part Four: Electricity Supply and Autocontrol
- Spinning: There are six temperature controlling sections for the extruder
- Extruder pressure controlling system
Part Five: Speed Adjusting System For Metering Pump
- The system is made of three parts: speed setting unit, velometer and motor
- Speed setting unit
- Public engineering
- Pressure controlling system for air dragging
- All the cables for auto controlling is put in the cable bridge so as to avoid the interference.They are directly from the controlling room to the local.
Effective Width | GSM Range | Max. Speed | Annual Capacity | Daily Capacity |
---|---|---|---|---|
2400MM Line | 8-80 | 500 m/min | 5700 Tons/Year | 16 Tons/Day |
3200MM Line | 8-80 | 500 m/min | 7500 Tons/Year | 21 Tons/Day |
4200MM Line | 8-80 | 500 m/min | 10000 Tons/Year | 28 Tons/Day |
SMS Nonwoven Fabric Making Machine Process Flow
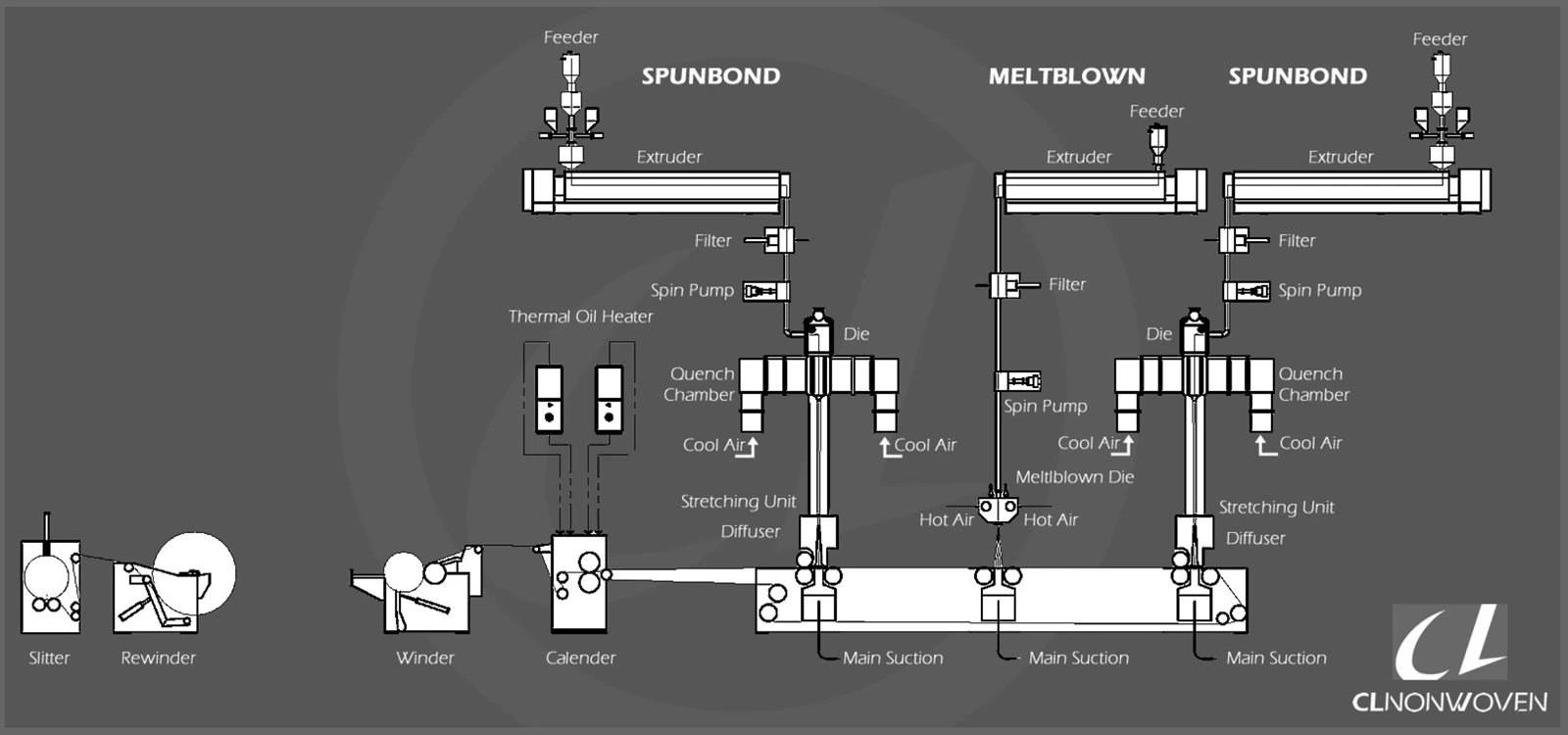