SMMS Nonwoven Fabric Making Machine
In 2006, CL constructed China's first SMMS line.
The SMMS fabric is composed of layers of spunbond and meltblown nonwoven fabrics, specifically arranged as spunbond, meltblown, meltblown, and spunbond. Compared to SMS, SMMS boasts a higher hydrostatic index, making it particularly well-suited for medical applications. It is commonly used in the production of surgical gowns, drapes, wraps, medical bed sheets, handwashing clothes, isolation gowns, lab coats, and more.
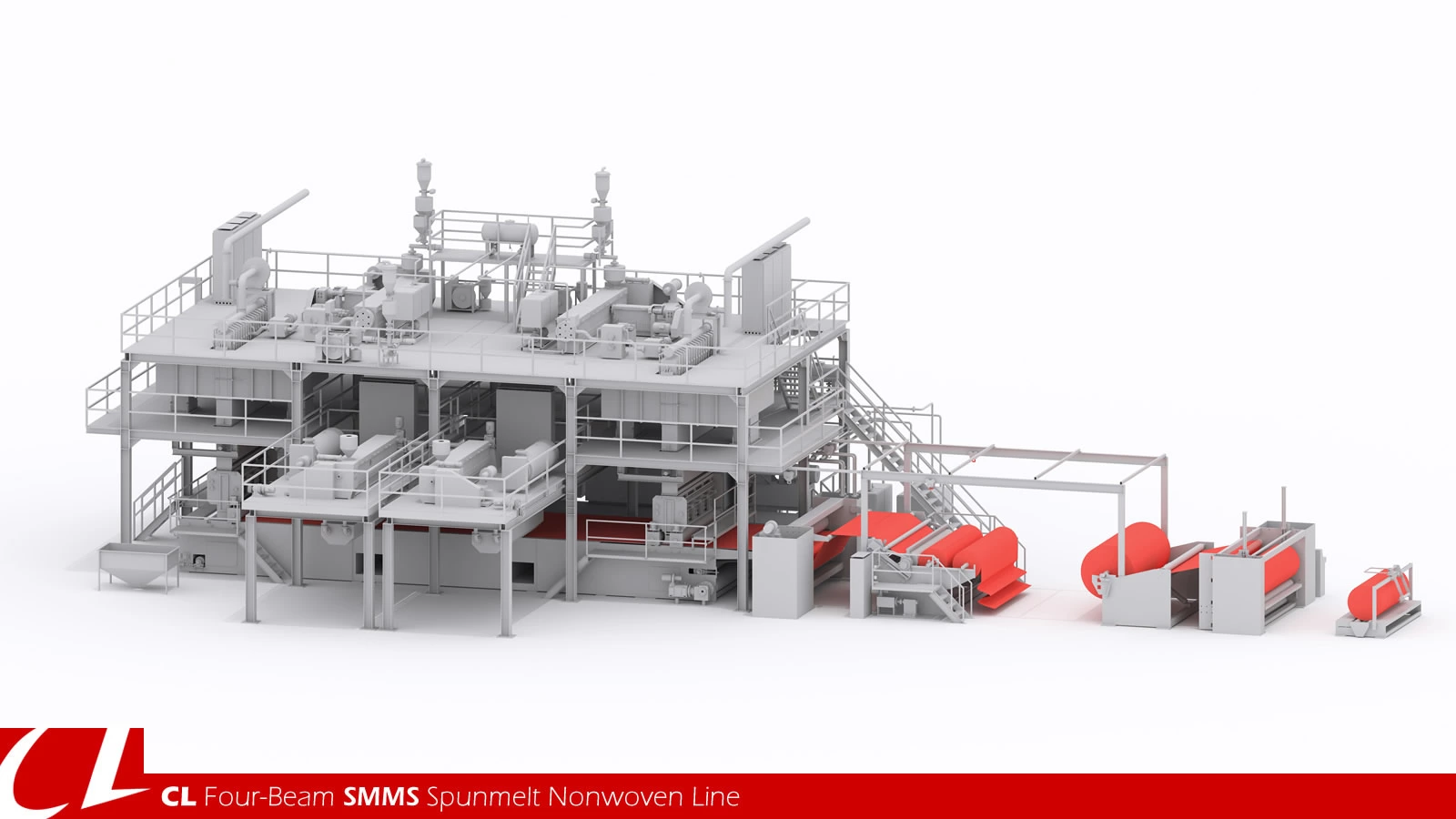
Technical Specification
Part One: The Design Conception Of This Project Is As Following:
PP chips ---- Blending and Feeding --- Melting in the Extruder --- Prefiltration Recycled Materials
Color masterbatch -- Spinning -- Cooling with the Side Wind -- Air Dragging Meltblown
Cooling with the Side Wind -- Air Dragging---Web forming -- Thermal bonding -- Winding -- Cutting -- End Products
Part Two: From The Figure It Can Be Seen That This Smms Spunmelt Line Include:
- Engineering: Electricity supply and distribution, Air conditioner and Cooling system.
- Spinning: PP chips feeding, Melt and Extruding, Spinning
- Web: Web forming,Thermal bonding and Winding
- Cutting: Semi-manufactured goods,Cutting, Packing
- Working time is calculated with four groups alternative
Part Three: Products Specification And Processing
- Products specification : Weight 9-80 g/sqm, width 1600/3200/4200MM
- Quality Standard: According to iternatipnal standard of SMMS spunmelt nonwovens.
- Spinning Feeding System: PP Chips, And colorful PP articles
- Extruder temperature:
- Spinning manifold:
- Metering Pump:
- Web forming
- Thermal bonding Width: 1600/2400/3200 mm Bonding area: As per fabric sample
Part Four: MM PART
- Raw material feeding system
- Masterbatch feeding
- Extruder
- Screen changer
- Spin pump
- Spinning die
- Nozzle
- Air heater
- Air compressor
- Down suction system
- Blower
Part Five: SS AND MM SHARE PARTS
- Winding
- Cutting
- Module cleaning
- Steel platform
Part Six: Electricity Supply and Autocontrol
- Dynamical electricity supply
- The auto controlling system of this project includes three parts: spinning, finishing and public engineering
- Spinning: There are six temperature controlling sections for the extruder.
- Extruder pressure controlling system
- Speed adjusting system for metering pump The system is made of three parts: speed setting unit, velometer and motor
Effective Width | GSM Range | Max. Speed | Annual Capacity | Daily Capacity | |
---|---|---|---|---|---|
2400MM Line | 8-80 | 550 m/min | 6800 Tons/Year | 19 Tons/Day | |
3200MM Line | 8-80 | 550 m/min | 9000 Tons/Year | 25 Tons/Day | |
4200MM Line | 8-80 | 550 m/min | 12000 Tons/Year | 33 Tons/Day |
SMMS Nonwoven Fabric Making Machine Process Flow
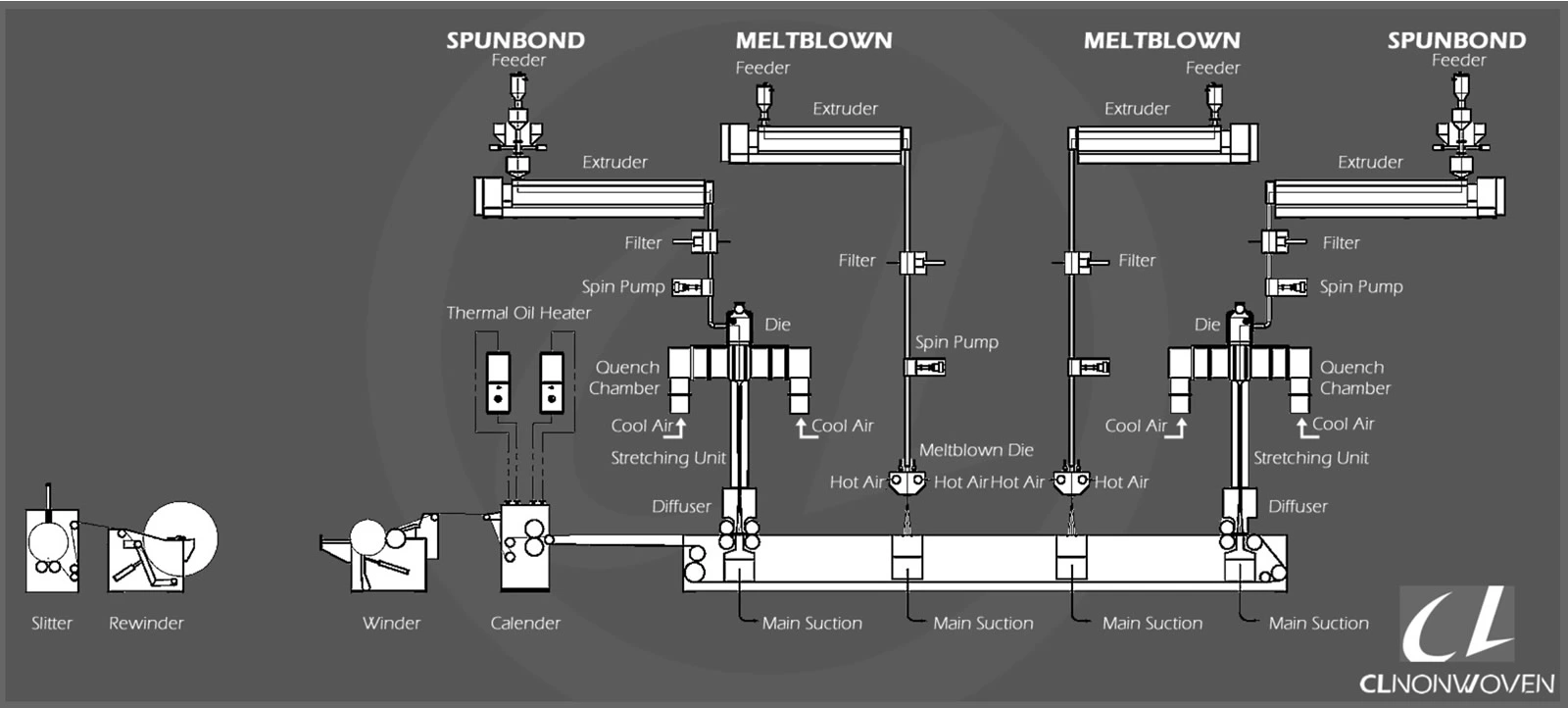