SS Nonwoven Fabric Making Machine
Double SS non-woven fabric boasts exceptional flexibility, making it perfect for use in the medical and hygiene sectors.
It is commonly utilized in the production of items like surgical caps, gowns, masks, protective clothing, surgical sheets, as well as the top and back sheets of baby diapers, among other products
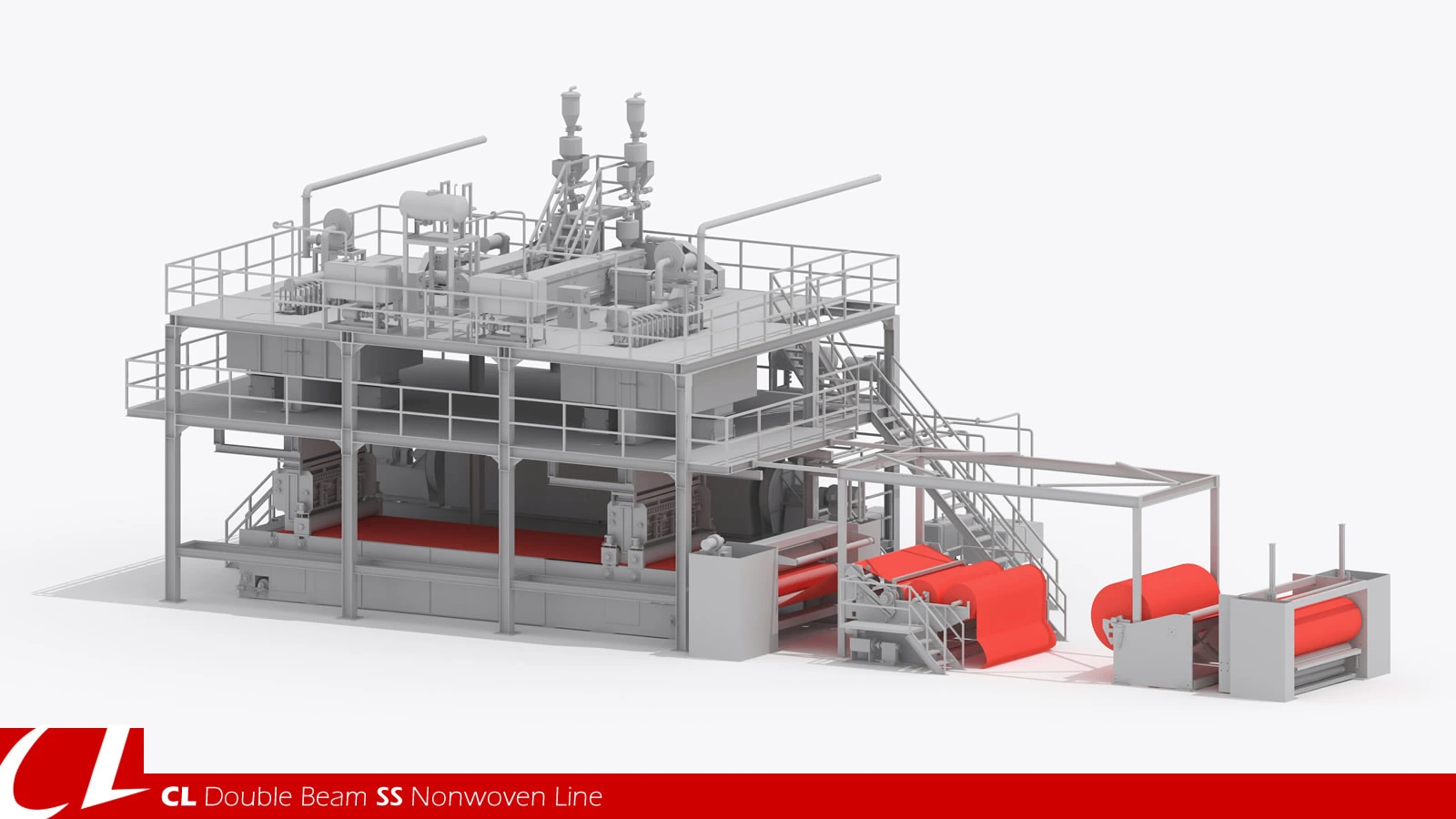
Technical Specification
Part One: The Design Conception Of This Project Is As Following
PP chips ---- Blending and Feeding --- Melting in the Extruder --- Prefiltration Recycled Materials
Masterbatch -- Spinning -- Cooling with the Side Wind -- Air Dragging -- Web forming -- Thermal bonding -- Winding -- Cutting -- End Products
From the figure it can be seen that this SS PP spunbond line includes the following parts:
- Engineering : Electricity supply and distribution, Air conditioner and Cooling system.
- Spinning : PP chips feeding, Melt and Extruding, Spinning
- Web: Web forming, Thermal bonding and Winding
- Cutting : Semi-manufactured goods, Cutting , Packing
- Working time is calculated with four groups alternative.
- Products specification : Weight 10-100 g/sqm, width 1600/2400/3200mm meters
- Quality Standard: According to the International standard of PP spunbond nonwovens
Part Two : Main Equipments
- Feeder air pump with the negative pressure, auto control for the up feeder
- Extruder : droven by AC motor, auto control for the temperature and pressure.
- Blending system for the colorful PP articles: metering and blending automatically and exactly so as to make the color and luster uniform.
- Spinning manifold: with single die and module with update technology.
- Heating system: heating extruder with electricity, heating the other parts with recycled heating system according to the customer requirement.
- Cooling system: this production using two sides air cooling system in order to make the full dragging and assure the fiber quality.
- Stretching unit system: drawing and making the fiber thin with the cooling air, adopt the update technology.
- Web former: collecting the fiber with the help of the negative pressure drawing so as to get the continuous web. It is made of gear change mechanism, frame, transmission apron and air suction system.
- Spin belt: carrying the web to the Calender for thermal bonding.
- Calender: mainly for web consolidation. There will be some deformation and melting in the web under the condition of high pressure of heating. So the bonding points come into being after cooling which makes the web to be a kind of nonwovens with certain property and appearance.
- Winder: mainly for winding the thermal bonding nonwovens to be a certain quantity. It is made of frame, friction roller, roller auto changing unit, rolling shaft, AC motor and controlling system
- Cutter: Mainly for cutting the nonwovens according to the request of the customer such as length, width and weight.
- Assembly cleaning: through annealing oven and microwave oven
Part Three : Electricity Supply and Auto control
- High and low voltage system is designed by the customer.
- Lighting and small dynamical system are the responsibility of the customer.
- For all the electric design and base construction, a set of transformer is used with the accessorial equipments.
Effective Width | GSM Range | Max. Speed | Annual Capacity | Daily Capacity |
---|---|---|---|---|
1600MM Line | 8-150 | 450 m/min | 3000 Tons/Year | 8 Tons/Day |
2400MM Line | 8-150 | 450 m/min | 4500 Tons/Year | 13 Tons/Day |
3200MM Line | 8-150 | 450 m/min | 6000 Tons/Year | 16 Tons/Day |
4200MM Line | 8-150 | 450 m/min | 8000 Tons/Year | 22 Tons/Day |
SS Nonwoven Fabric Making Machine Process Flow
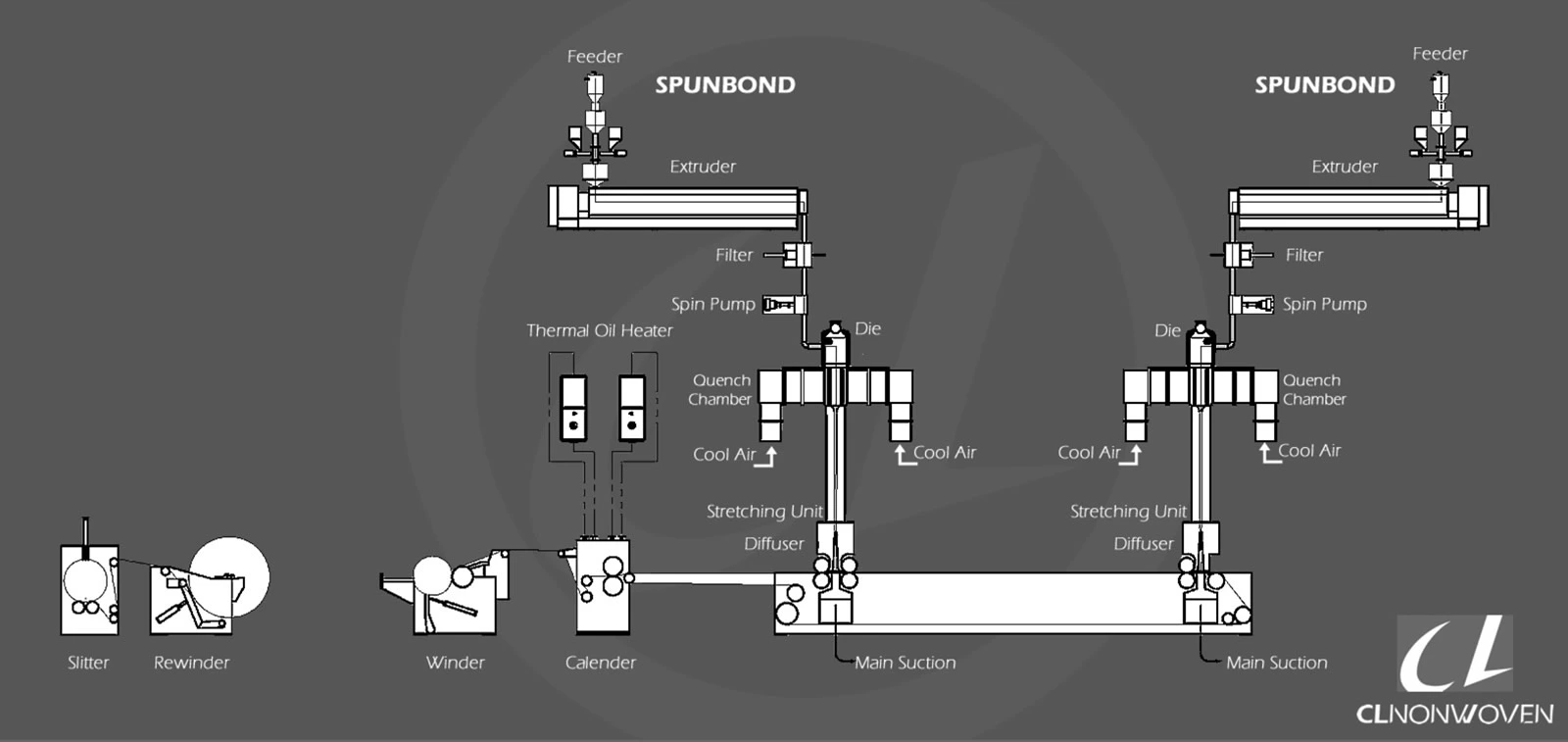