PET Nonwoven Line
In 2005, CL developed and built China's pioneering PET production line.
This advanced equipment utilizes recycled PET (RPET), PET, and PLA as raw materials, offering customers efficient and eco-friendly production solutions that contribute to environmental conservation efforts on Earth
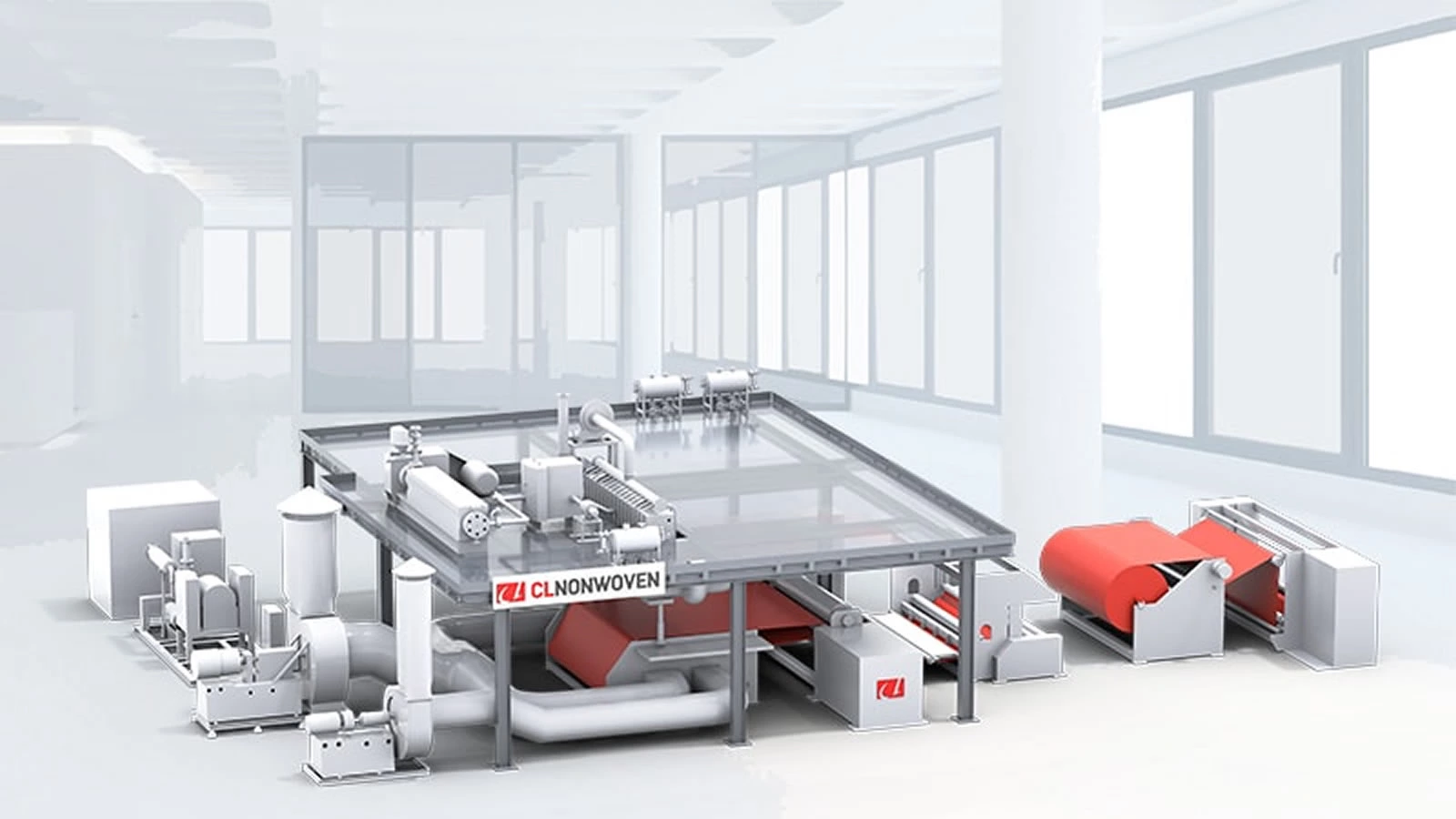
Pet/ rPet Nonwoven Fabric Making Machine Technical Specification
Model | Effective Width | Fabric Gsm | Machine Speed | Raw Material | Capacity |
1600 PET | 1600 | 15-280gsm | 150m/min | PP Chips | 5 Ton/Day |
2400 PET | 2400 | 15-280gsm | 150m/min | PP Chips | 7.5 Ton./Day |
3200 PET | 3200 | 15-280gsm | 150m/min | PP Chips | 10 Ton/Day |
PRODUCTION LINE OVERVIEW
This nonwoven fabric manufacturing machine is dedicated to producing PET nonwoven fabrics through spinning, web forming, and thermal bonding processes. It primarily utilizes PET as the core raw material, complemented by additives like color master batches. The production line excels in producing PET spunbond nonwoven fabrics in diverse colors and with varied properties, catering to a wide range of applications.
GENERAL REQUIREMENTS OF THE MAIN EQUIPMENT OF PET LINE SYSTEM
1.Crystal and dry system
2 Masterbatch drying system
The masterbatch was manually added into the drying device in order to dry it.
3 Masterbatch metering, mixing device feeding system
The fully dried masterbatch is added and stored in the hopper above the feeding screw.
4 Screw extruder
Function and composition of the equipment: this device is mainly to squeeze and melt the PET chips, composed of transmission gear, reducer, screw, mixing head, sleeve, ceramic heater, frame, etc.and it’s equipped with automatic temperature control, cooling system and alarm system. The main transmission adopts AC frequency conversion control. The temperature control of each area adopts the temperature control module, solid state relay and Pt 100 platinum thermal resistance to form a temperature control closed-loop system.
5 Vertical cylinder melt filter
Cylinder filter is a vertical double-barrel switching melt filter, four sets of valves are controlled separately, and two sets of filter chambers can be used in parallel to double the production capacity; Using metal hard seal, which is reliable and long-life; The operation is easy and safe.
6 Spin pump and drive
Type: gear pump
7 Spinning die body (1 set, CL Latest Design)
8 Monomer suction device (1 set, CL Latest Design)
Double row and parallel with multiple tubes
9 Quenching chamber device (1 set, CL Latest Design)
Adopts new lateral blowing structure. Main frame is made of aluminum. Stainless steel sealing plate has thermal insulation function.
10 Stretching unit (1 set, Kasen, Japan)
Adopts the new extension air duct structure with thermal insulation.
11. Web former (1 set, CL Latest Design)
Spin Belt: Two Pieces,One for use during commissioning, And the other one for use after commissioning is complete
1.2 Two-roll calender
Roller’s form: the upper roller is an embossing roller, and the lower roller is a smooth roller. The effective pattern width of the embossing roller is 3850mm. The width of smooth roller is 3600mm.
1.3 Winder
Effective working width: 3500mm